Make a Metal Sword Without a Forge: This seemingly impossible feat is explored in this in-depth look at alternative swordmaking techniques. Imagine crafting a blade of steel without the traditional forge, harnessing different heat sources and shaping methods. We’ll delve into the historical context, materials, and crucial safety considerations, potentially revealing a new approach to this age-old craft.
The article will explore the concept, outlining the fundamental principles of metalworking and contrasting them with traditional methods. We’ll examine alternative heat sources and techniques, analyze the necessary metal selection and preparation, and detail the shaping and tempering processes. Safety precautions and potential hazards will also be thoroughly discussed.
Introduction to the Concept
The concept of crafting a metal sword without a forge, while seemingly fantastical, explores the boundaries of traditional metalworking techniques. It challenges the conventional understanding of swordsmithing, potentially revealing hidden possibilities and alternative methods for shaping and hardening metal. This exploration delves into the theoretical possibilities of such a process, examining the materials, methods, and underlying principles.This investigation examines the feasibility of forging high-quality swords using alternative heat sources, potentially uncovering ancient or overlooked techniques.
It will consider the fundamental materials, analyze the required smithing techniques, and assess the impact of different heat treatment methods on the final product’s quality.
Historical Examples of Non-Forge Swordmaking
While documented examples of swordmaking without a traditional forge are scarce, some historical accounts hint at alternative techniques. Some ancient cultures likely employed methods using intense heat from natural sources, such as volcanic vents or concentrated solar energy, to achieve the necessary temperatures for metalworking. These methods were likely limited by the availability and controllability of these heat sources, which would have heavily impacted the scale and efficiency of production.
However, these methods may have been more prevalent in specific geographic regions or historical periods. The lack of readily available written records, particularly from those cultures, often makes it difficult to definitively determine the exact methods employed.
Fundamental Materials
The fundamental materials for swordmaking, irrespective of the method, remain largely the same. High-carbon steel, often alloyed with other metals for enhanced properties, is a crucial component. The specific alloying elements and their proportions significantly impact the sword’s hardness, toughness, and durability. Other materials, like the handle materials, will be needed as well. Wood, leather, or bone are frequently used for handles.
The choice of these materials directly impacts the sword’s balance, ergonomics, and aesthetic appeal.
Basic Principles of Metalworking
The core principles of metalworking remain constant, regardless of the heat source. Smithing techniques, like hammering, forging, and annealing, are crucial for shaping the metal into the desired form. Precise control over the heating and cooling processes is paramount. The resulting hardness and toughness depend on the specific heat treatment applied. Crucially, heat treatment methods like quenching and tempering are vital in achieving the optimal balance between hardness and toughness in the final product.
Comparison of Traditional and Alternative Swordmaking Methods
Feature | Traditional Forge Method | Alternative Method (e.g., Solar/Natural Heat) |
---|---|---|
Heat Source | Fuel-fired forge | Solar concentrator/volcanic vent/etc. |
Temperature Control | Precise control through regulating fuel supply and air flow. | Limited control; reliance on natural variations and precise timing. |
Shaping Techniques | Hammering, forging, and annealing, with the use of various tools. | Possible use of specialized tools, adapted to the constraints of the alternative heat source. |
Alternative methods, while potentially less controlled, may offer unique advantages. The limitations imposed by the chosen heat source, however, would dictate the constraints on the process and the potential end result.
Alternative Heat Sources and Techniques
Crafting a sword without a forge requires innovative approaches to achieving the necessary heat for metalworking. This section explores various alternative heat sources and the associated techniques, considering safety, efficiency, and the required equipment. These methods, while not ideal replacements for a traditional forge, can offer valuable insights into the potential for more sustainable and accessible metalworking practices.This exploration will detail different methods of achieving high temperatures outside a conventional forge environment, focusing on the advantages and disadvantages of each, the required equipment, and comparisons of their efficiency and safety.
Solar Heat
Harnessing the power of the sun for metalworking presents an intriguing, albeit limited, option. Concentrated solar energy, using mirrors or lenses to focus sunlight onto a target, can generate intense heat. This method is most effective during periods of strong sunlight and in locations with high solar irradiance.
- Advantages: Renewable energy source, potentially low operating costs (excluding initial investment).
- Disadvantages: Dependent on weather conditions, limited operating hours, potentially high initial equipment cost, large space requirements.
- Equipment Required: Large parabolic mirrors or lenses, specialized temperature-resistant materials for the heat-absorbing surface, and appropriate safety shielding.
- Safety Precautions: Extreme care must be taken to prevent burns and eye injuries. Direct exposure to concentrated solar radiation can be dangerous. Adequate protective eyewear and clothing are essential.
Gas Heat
Gas burners offer a versatile alternative heat source for smithing. Propane, butane, or other combustible gases can be used to achieve high temperatures. This method is more reliable than solar heat, as it is less dependent on weather conditions.
- Advantages: Relatively portable and controllable, offers more consistent heating compared to solar methods, readily available fuel.
- Disadvantages: Requires fuel supply, potential for gas leaks, requires careful management of the flame, potential for soot and fumes.
- Equipment Required: Gas tanks, high-temperature gas burners, and appropriate ventilation systems.
- Safety Precautions: Regularly check gas connections for leaks, use appropriate ventilation to prevent carbon monoxide buildup, wear appropriate safety gear, and be mindful of potential ignition sources.
Electric Heat, Make a Metal Sword Without a Forge
Electric resistance heating methods, employing elements like ceramic heaters, are increasingly popular due to their precise temperature control. They provide a predictable and controllable heating process, making them useful for specialized tasks.
- Advantages: Highly controllable temperature, minimal pollution, readily available electricity.
- Disadvantages: High initial equipment cost, potential for electrical hazards if not handled correctly.
- Equipment Required: Electric resistance heating elements, specialized temperature-resistant materials for the heat-absorbing surface, appropriate electrical safety equipment, and voltage regulators.
- Safety Precautions: Ensure proper electrical grounding, use appropriate insulation materials, and follow electrical safety guidelines to prevent shocks and fires.
Table: Alternative Heat Sources and Techniques
Heat Source | Technique | Equipment Required | Safety Precautions |
---|---|---|---|
Solar Heat | Concentrated solar energy | Parabolic mirrors/lenses, temperature-resistant materials | Eye protection, appropriate clothing, fire prevention measures |
Gas Heat | Gas flame heating | Gas tanks, high-temperature burners, ventilation | Gas leak checks, adequate ventilation, fire safety |
Electric Heat | Electric resistance heating | Resistance elements, insulation, voltage regulators | Electrical safety, proper grounding, insulation |
Metal Selection and Preparation
Forging a sword, even without a traditional forge, requires careful consideration of the metal’s properties and preparation. Choosing the right metal and properly preparing it directly impacts the sword’s strength, durability, and aesthetic appeal. The absence of a forge necessitates alternative methods for achieving the desired heat treatments, thus influencing the selection process.The process of selecting and preparing metal for a sword, outside of a traditional forge, demands a deeper understanding of metallurgical principles.
Understanding the properties of various metals and their suitability for sword-making is crucial. Careful preparation techniques, like cleaning and annealing, are vital to ensure the metal’s quality and prevent defects in the finished blade. The purity of the metal is also paramount, as impurities can compromise the blade’s performance and longevity.
Ever wondered how to craft a metal sword without a proper forge? It’s surprisingly achievable with some ingenuity and the right materials. While researching techniques, I stumbled upon this fascinating exploration of seemingly mundane suburban landscapes – suburban lawns suburban lawns. The intricate patterns and seemingly endless repetition reminded me of the careful craftsmanship needed for forging a blade, even without a traditional forge.
Back to the sword project – I’m excited to dive deeper into the possibilities.
Suitable Metals for Non-Forge Swordmaking
Various metals, with different properties, can be considered for sword creation outside a forge environment. Suitable metals must be workable using alternative heating methods. Iron, steel, and even some non-ferrous metals can be viable options, depending on the desired outcome.
- Iron: Iron, while not as strong as steel, can be worked with suitable heat sources. Its malleability allows for shaping, and its relatively low melting point makes it easier to work with using methods like induction heating or solar furnaces. However, pure iron lacks the hardness and toughness needed for a high-quality sword. The addition of carbon or other elements to make steel is often essential.
- Steel: Steel alloys, containing varying percentages of carbon, are the most common choice for swordmaking. The carbon content directly impacts the hardness and toughness of the steel. Different types of steel will respond differently to various heat treatments and preparations, so careful selection is essential. High-carbon steels, for instance, are ideal for achieving a hard, sharp edge.
However, these can be more brittle than lower-carbon options.
- Copper: While not traditionally associated with swordmaking, copper can be used for decorative or ceremonial purposes. Its malleability and aesthetic qualities can be desirable for certain types of blades. However, its lower hardness and strength limit its use for functional swords.
- Aluminum: Aluminum is exceptionally lightweight, but its low strength and hardness make it unsuitable for swordmaking. Its lack of resilience would result in a fragile blade.
Metal Purity and Preparation
Metal purity significantly influences the sword’s quality. Impurities can lead to inconsistencies in the blade’s structure and performance. Furthermore, impurities can create weaknesses and vulnerabilities in the metal, impacting its ability to withstand stress and impact.
Ever wondered how to make a metal sword without a forge? Turns out, crafting impressive blades requires more than just raw materials. While some might be inspired by the latest music charts, like Drake recently topping Justin Bieber as Spotify’s most streamed artist here , the reality is that blacksmithing takes meticulous skill and the right tools.
Even without a forge, you can still explore the art of swordmaking, but the journey will demand dedication and creativity.
- Purification Methods: Methods for purifying metal outside a forge can vary. Methods like refining with alternative heating sources, and careful selection of raw materials can be critical in reducing impurities.
- Importance of Purity: High purity minimizes flaws, resulting in a more consistent and reliable blade. This translates to a stronger, sharper, and more durable sword. Lower purity metals are more prone to cracking or breaking under stress.
Comparing Metal Types for Non-Forge Swordmaking
Different metals offer various advantages and disadvantages when creating a sword without a forge. Choosing the right metal depends on the intended use of the sword and the available resources. Consider factors like strength, hardness, ductility, and the required heat treatments.
Metal | Properties | Suitability for Swordmaking |
---|---|---|
Mild Steel | Relatively low carbon content, good ductility, moderate hardness. | Suitable for basic blades, less demanding applications. |
High-Carbon Steel | High carbon content, high hardness, high strength, but potentially brittle. | Excellent for blades requiring a very sharp edge but demanding precise heat treatment. |
Iron | Low carbon content, soft, relatively low melting point. | Suitable for simple blades but needs further treatment to improve strength. |
Copper | High ductility, good for shaping, relatively low hardness. | Not suitable for functional swords, more appropriate for decorative purposes. |
Shaping and Tempering Methods
Crafting a sword without a forge demands meticulous control over heat and shaping techniques. This section details the methods and procedures for achieving the desired form and resilience in a blade, crucial for its performance and durability. The absence of a forge necessitates alternative heat sources and techniques, demanding a deep understanding of the metal’s properties and behavior under different conditions.Achieving a functional sword requires a comprehensive understanding of metalwork principles, even without traditional forging techniques.
The goal is to precisely shape the metal into a sword form, and then to harden and temper it for durability and edge retention. This meticulous process necessitates an understanding of the metal’s thermal properties and the specific heat treatment required to transform raw material into a weapon.
Shaping Techniques
Various shaping techniques are available to craft a sword form without a forge. These techniques, while not replacing the precision of a forge, can be used to create a satisfactory sword. The choice of technique depends heavily on the availability of tools and the metal being used.
- Hand-hammering and Anvil Shaping: This method involves repeatedly striking the metal on an anvil using hammers of varying sizes. This method allows for controlled shaping and refinement of the blade’s form. The process is iterative, requiring numerous hammering sessions to sculpt the desired contours and achieve a balanced weight distribution. Skilled artisans utilize this technique to mold the metal into the desired shape for the blade, handle, and pommel.
- Cold Shaping and Bending: Some metals, particularly softer varieties, can be shaped by bending and cold hammering. This method is ideal for creating simple forms or pre-designed patterns on the blade, especially for decorative or functional purposes. While the metal doesn’t reach the high temperatures necessary for significant structural alteration, it allows for the initial design and form to be established.
Step-by-Step Blade Creation
A step-by-step procedure for creating a sword blade without a forge, using hand-hammering and anvil shaping, is as follows:
- Preparation: Ensure the metal is clean and free from contaminants. Mark the desired blade shape on the metal sheet.
- Initial Shaping: Using a hammer and anvil, begin to gradually shape the metal into a basic blade form, focusing on the overall shape and thickness. Carefully remove excess metal to achieve the desired thickness and taper. Ensure even distribution of the metal. Repeated hammering should occur in the same direction to minimize unwanted distortions.
- Refinement: Refine the blade’s shape using the hammer and anvil, focusing on the edges, tip, and back of the blade. Achieving the desired curvature and taper is essential. This stage requires patience and precision.
- Hardening: Heat the blade to the correct temperature using an alternative heat source (e.g., charcoal fire). Precise temperature control is crucial to prevent overheating or underheating.
- Tempering: Once hardened, rapidly cool the blade. This process may involve plunging the blade into water or oil. Tempering involves reheating the blade to a specific lower temperature to achieve the desired hardness and toughness.
Achieving Hardness and Durability
The hardness and durability of the blade are determined by the combination of the metal’s inherent properties and the heat treatment. The hardness is achieved by heating the metal to its critical temperature, then quenching (cooling rapidly). Tempering further modifies the hardness, increasing toughness and resistance to impact.
Importance of Tempering
Tempering is crucial for balancing hardness and toughness in the blade. Excessive hardness can lead to brittleness, making the blade prone to chipping or breaking. Proper tempering ensures that the blade is hard enough to hold an edge but tough enough to resist impact damage. Achieving the right balance is critical for the sword’s longevity and effectiveness.
Flow Chart
A flow chart illustrating the shaping and tempering process is presented below.
Start | V [Metal Preparation] --> [Initial Shaping] --> [Refinement] --> [Hardening] --> [Rapid Cooling] --> [Tempering] --> [Final Inspection] | V End
Safety Precautions and Considerations
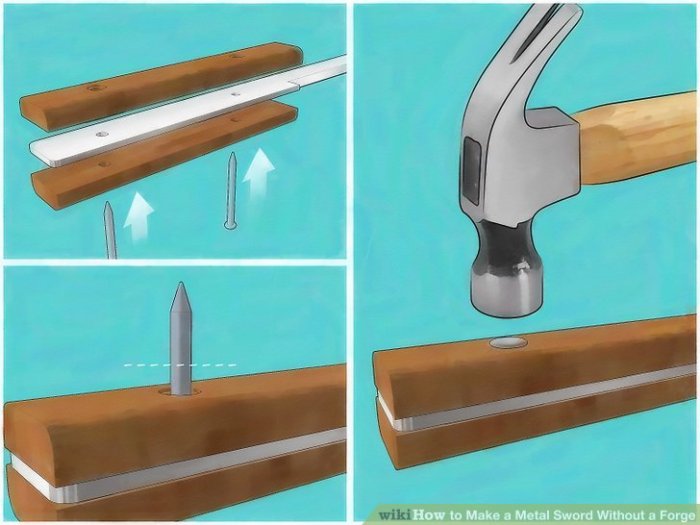
Forging a sword, even with alternative methods, requires meticulous attention to safety. Improper techniques or inadequate precautions can lead to severe injuries, from burns and cuts to potential fire hazards.
This section details crucial safety measures to mitigate these risks and ensure a safe and productive forging experience.
Alternative heat sources and techniques, while offering advantages in terms of accessibility and control, introduce new safety concerns. Carefully following the specific safety guidelines for each method is paramount to avoid accidents.
Potential Hazards of Alternative Heat Sources
Using alternative heat sources like propane torches, induction heating, or even concentrated sunlight introduces specific risks. Propane torch use necessitates proper ventilation to prevent carbon monoxide buildup, while induction heating requires careful insulation to prevent electrical shocks. Improper handling of these tools can result in burns, fire, or electrical hazards.
Safety Precautions for Specific Techniques
Several safety precautions are crucial for each alternative forging technique. For instance, when using a propane torch, always work in a well-ventilated area. Ensure the torch is properly maintained and the fuel supply is secure. For induction heating, use appropriate insulation materials to prevent electrical shock, and ensure the equipment is grounded correctly.
Importance of Proper Ventilation
Adequate ventilation is critical to prevent the inhalation of harmful fumes or gases generated during the heating process. Fumes from propane, or even metal oxides, can cause respiratory issues. The use of exhaust fans, or working outdoors in well-ventilated areas, is highly recommended.
Personal Protective Equipment (PPE)
Proper personal protective equipment (PPE) is essential to protect against burns, flying sparks, and other potential hazards. Wear heat-resistant gloves, aprons, and eye protection (such as welding goggles). A fire-resistant long-sleeved shirt and pants are highly recommended for added protection.
Handling Hot Metal
Handling hot metal requires specific procedures to prevent burns. Use heat-resistant tongs or pliers to manipulate the metal. Never touch hot metal directly with your bare hands. Allow the metal to cool gradually, ensuring proper ventilation to prevent further risks.
Making a metal sword without a forge is surprisingly doable, though it’s definitely not for the faint of heart. You’ll need a lot of patience and a good understanding of metallurgy, but the results can be pretty cool. It’s like a real-life crafting challenge, and honestly, I’ve been listening to “Up out my face ft nicki minaj” up out my face ft nicki minaj while I’m hammering away at it.
The music really gets me going. Once you get the hang of it, making a sword from scratch becomes incredibly rewarding.
Safety Measures by Stage
Stage | Safety Measures | PPE |
---|---|---|
Stage 1: Preparation | Inspect all equipment for damage or malfunction. Ensure adequate ventilation. | Safety glasses, work gloves, fire-resistant clothing. |
Stage 2: Heating | Maintain a safe distance from the heat source. Follow specific safety instructions for the chosen heat source. | Heat-resistant gloves, welding goggles, long-sleeved shirt and pants. |
Stage 3: Shaping | Use appropriate tools and techniques. Be aware of potential flying sparks. | Welding goggles, fire-resistant gloves, safety glasses. |
Stage 4: Cooling and Tempering | Allow the metal to cool gradually. Avoid sudden temperature changes. | Heat-resistant gloves, safety glasses. |
Illustrative Examples: Make A Metal Sword Without A Forge
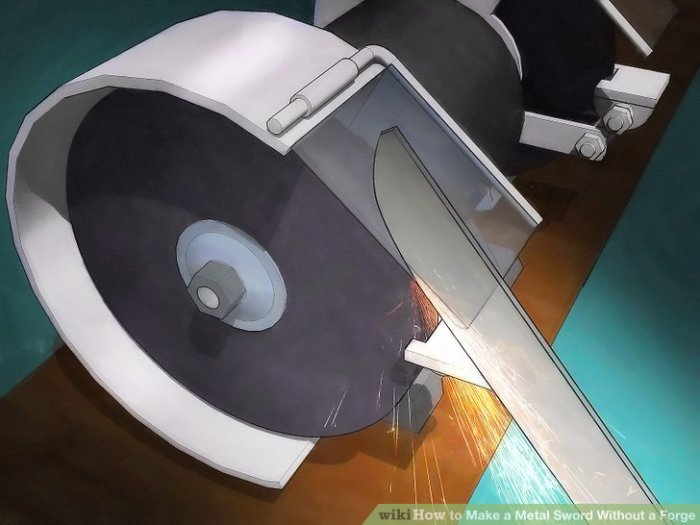
Crafting a sword without a traditional forge presents a fascinating array of possibilities, each with its own unique challenges and rewards. These alternative methods, while often less controlled than traditional techniques, allow for experimentation and the exploration of unusual materials and techniques. The following examples showcase some successful and notable attempts at creating swords using unconventional approaches.
The successful creation of a sword using alternative methods often hinges on understanding the properties of the chosen materials, adapting techniques to the specific heat source, and carefully controlling the forging process. Careful consideration of the specific heat source and the properties of the chosen metal is crucial for success.
Examples of Swords Crafted Using Alternative Heat Sources
Alternative heat sources offer a range of possibilities, each with its own set of advantages and disadvantages. For example, induction heating can provide precise temperature control, while propane torches offer a portable and readily available option. The choice of heat source directly impacts the shaping and tempering process.
- Induction Heating Method: Using an induction coil and a specialized power supply, a blacksmith could heat a piece of high-carbon steel. The precise control over temperature allows for more intricate shaping, such as fine details on the blade’s edge. This method often yields a high degree of repeatability and control, enabling the crafting of highly symmetrical and refined blades.
The final product exhibits a mirror-like polish and precise geometry, reflecting the precision of the induction heating process. Challenges include the need for specialized equipment, which can be expensive, and the potential for uneven heating if the coil is not properly positioned.
- Propane Torch Method: A propane torch, a more readily available option, provides a portable heat source. This method is suitable for smaller projects and outdoor forging. A key advantage is its accessibility, but it requires more skill and experience to maintain precise temperature control. Results may vary based on the consistency of the flame and the blacksmith’s expertise.
The swords crafted using propane torches often display a more rustic, hand-forged aesthetic, with variations in texture and surface finish. This method allows for a greater degree of improvisation and flexibility, but precise control over the heating process can be challenging.
Metal Selection and Preparation
Choosing the correct metal for the intended sword is paramount. Different metals respond differently to heat treatment, and the resulting properties will influence the blade’s durability and sharpness. Preparing the chosen metal involves cleaning, refining, and possibly alloying it to achieve the desired characteristics.
- High-Carbon Steel: High-carbon steel, known for its hardness and sharpness, is a popular choice for swords. Its ability to be tempered to a high level of hardness is crucial for a functional blade. Careful heat treatment is necessary to avoid cracking or warping. The resulting sword displays a hard, sharp edge that can maintain its edge well over time.
- Wootz Steel: Wootz steel, a historical Indian steel, is famous for its unique layered structure and remarkable properties. While more difficult to work with, the resulting blades often demonstrate exceptional sharpness and durability. The distinct layered structure and varied colorations of the blade are visually striking. Challenges include the difficulty in replicating the ancient methods for producing Wootz steel.
Shaping and Tempering Methods
The shaping and tempering methods employed directly influence the sword’s final form and performance. Careful control of heat and hammering is critical to achieve the desired shape and hardness.
- Hammering Techniques: The method of hammering is critical for shaping the blade and removing impurities. Different hammering techniques, such as fullering and beveling, can impart unique characteristics to the blade’s shape and form. The final product may exhibit subtle variations in the blade’s texture and surface due to the hammering process.
- Tempering Processes: Tempering, a critical step, involves controlled cooling to achieve the desired hardness and toughness balance. Precise control over the cooling rate is essential to prevent cracking and ensure the sword’s longevity. The final product exhibits a hardness and toughness profile that allows for sharp edges and a resilient blade.
Epilogue
Crafting a metal sword without a forge is a fascinating endeavor, demanding meticulous attention to detail and a thorough understanding of the principles of metalworking. While traditional methods are deeply rooted in history, alternative techniques offer intriguing possibilities. The article explores the feasibility and challenges of this unusual approach, ultimately revealing the intricate steps and potential hazards involved in this unique metalworking journey.
Hopefully, this guide will inspire further exploration and experimentation for those interested in forging their own blades.
Leave a Reply